The Indian cement industry is one of the largest in the world, both in terms of production and consumption. The sector has been experiencing steady growth due to infrastructure development, housing projects, and increased demand from the real estate sector. Fueled by the demand for infrastructure projects, housing, and urban development, major players like Ultratech Cement, ACC, and Ambuja Cements have played pivotal roles in shaping the industry landscape. As India continues its trajectory of growth, the cement industry remains a vital player in meeting the burgeoning demands of a rapidly developing nation.
Enhancing the audit process within the cement sector poses a distinctive challenge, demanding a meticulous examination of specific procedures and processes inherent to cement production. The auditor's proficiency lies in comprehending the intricacies of cement manufacturing, discerning the unique activities involved, and navigating the sector-specific challenges. A nuanced understanding of the complexities within the production chain is essential for auditors to effectively scrutinize and verify the various facets integral to the cement industry's financial and operational integrity.
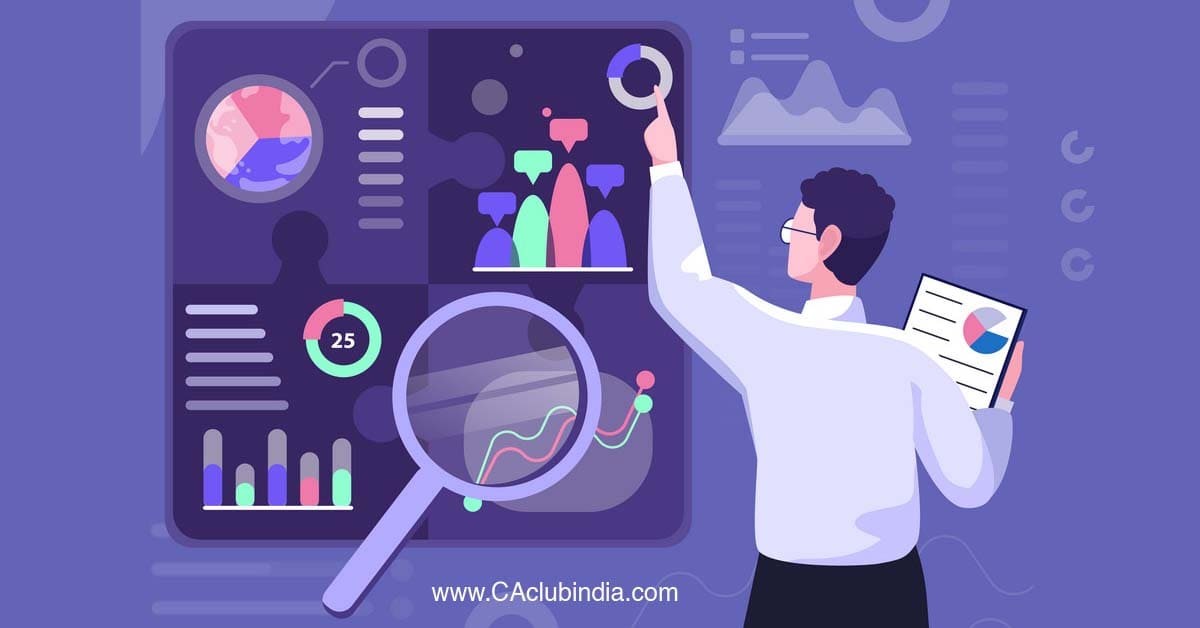
Following is the overview process of the cement industry
Mining
The cement manufacturing process starts from the mining of limestone, which is the main raw material for making cement. Limestone is excavated from open cast mines after drilling and blasting and loaded on to dumpers which transport the material and unload into hoppers of the limestone crushers.
Stacking Crushing & Reclaiming of Limestone
The Lime stone Crushers crush the limestone onto a belt conveyor which takes it to the stacker via the Bulk material analyser. The material is stacked in longitudinal stockpiles. Limestone is extracted transversely from the stockpiles by the reclaimers and conveyed to the Raw Mill hoppers for grinding of raw meal.
Crushing Stacking & Reclaiming of Coal
The process of making cement clinker requires heat. Coal is used as the fuel for providing heat. Raw Coal received from the collieries is stored in a coal yard. Raw Coal is dropped on a belt conveyor from a hopper and is taken to and crushed in a crusher. Crushed coal discharged from the Coal Crusher is stored in a longitudinal stockpile from where it is reclaimed by a reclaimer and taken to the coal mill hoppers for grinding of fine coal.
Raw Meal Drying/Grinding & Homogenization
Reclaimed limestone along with some laterite stored in their respective hoppers is fed to the Raw Mill for fine grinding. The hot gasses coming from the clinkerization section are used in the raw mill for drying and transport of the ground raw meal to the Electrostatic Precipitator / Bag House, where it is collected and then stored and homogenized in the concrete silo. Raw Meal extracted from the silo (now called Kiln feed) is fed to the top of the Preheater for Pyro processing.
Clinkerisation
Cement Clinker is made by pyro processing of Kiln feed in the preheater and the rotary kiln. Fine coal is fired as fuel to provide the necessary heat in the kiln and the Precalciner located at the bottom of the 5/6 stage preheater. Hot clinker discharged from the Kiln drops on the grate cooler and gets cooled. The cooler discharges the clinker onto the pan / bucket conveyor and it is transported to the clinker stockpiles / silos. The clinker is taken from the stockpile / silo to the ball mill hoppers for cement grinding.
Cement Grinding & Storage
Clinker and Gypsum (for OPC) and also Pozzolana (for PPC) are extracted from their respective hoppers and fed to the Cement Mills. These Ball Mills grind the feed to a fine powder and the Mill discharge is fed to an elevator, which takes the material to a separator, which separates fine product and the coarse. The latter is sent to the mill inlet for regrinding and the fine product is stored in concrete silos.
Packing
Cement extracted from silos is conveyed to the automatic electronic packers where it is packed in 50 Kgs. Polythene bags and dispatched in trucks.
In addition to the standard audit procedures applicable to various industries, the auditor must incorporate specific steps tailored to the nuances of the Cement industry. The following highlights key audit measures uniquely crafted to address the intricacies and challenges inherent to the cement manufacturing sector.
Production Process
Kiln operations
- Verify the parameters of the kiln including the temperature, residence time and rotation speed.
- Assess the efficiency of fuel combustion and alternative fuel consumption
Clinker Production
- Assess proper functioning of clinker cooler.
- Verify the quality of clinker produced, including chemical composition and clinker grindability.
- Assess the efficiency of the cooling process and controls over clinker quality.
Cement grinding
- Confirm that cement mill operates within the designed parameters
- Calculate the efficiency of the cement grinding process
- Review control over the cement particle size
Packaging and Dispatch
- Confirm that cement packaging and labeling comply with regulatory requirements.
- Review controls over the loading and dispatch of finished goods.
- Verify the accuracy of dispatch records and documentation.
Property, Plant and Equipment (PPE)
- Verify the valuation of the quarry reserves. Do they align with geographical survey and industry norms.
- Evaluate the company’s estimation of quarry reserves and assess the appropriateness of any requirement for impairment of the quarry reserves
- Assess the risk of impairment of assets for kiln, grinding mills and other machinery
- Verify the impairment testing methodology and assumptions used by management.
- Confirm the ownership and valuation of land and mineral rights
- What is the accounting treatment of payment related to land use or the extraction rights.
Inventory Management
- Verify the process for procuring raw materials such as limestone, clay, and gypsum
- Confirm the reliability of supplier and assess the risk related to supply chain.
- Review any long-term contracts, specially those related to major supply agreements and asses the accounting treatment of these long-term contracts
- Verify the quantities and valuation of raw materials such as limestone, clay, and gypsum.
- Confirm that the composition of raw materials aligns with production requirements and quality standards.
- Assess the adequacy for provision for slow-moving or obsolete inventory
- Evaluate the quality control processes, including testing of raw material, intermediate process and finished goods by adherence to the industry standard for cement industry
- Confirm the quantities and valuation of finished goods like cement bags and bulk cement.
Environmental compliances
- Review the company’s compliance with Industry regulations
- Verify the accuracy of monitoring and reporting of kiln emissions.
- Confirm compliance with emission standards for pollutants such as particulate matter, nitrogen oxides (NOx), sulfur dioxide (SO2), and carbon monoxide (CO).
- Confirm compliance with regulations regarding land reclamation and rehabilitation of extraction sites.
- Evaluate the effectiveness of dust control measures during the cement manufacturing process.
- Assess water usage practices, especially in the context of cooling systems and dust suppression.
- Confirm that the company is reporting environmental data as required by regulatory authorities.
- Review the handling and disposal of waste generated during the manufacturing process.