Production completion
The very first step is to check whether production is fully completed or not for the particular period/batch/job/process/work, etc. Sometimes we need to close the process during the production; this situation may arise where we need to do the closing month-end or year-end closing procedures for the books closure. In case we need to close the run closing procedure during the process or before completing the full production, then we need to calculate the stages or percentage of completion of the production process, calculating the percentage of completion of production required to calculate the work in progress data at the end of a particular period.
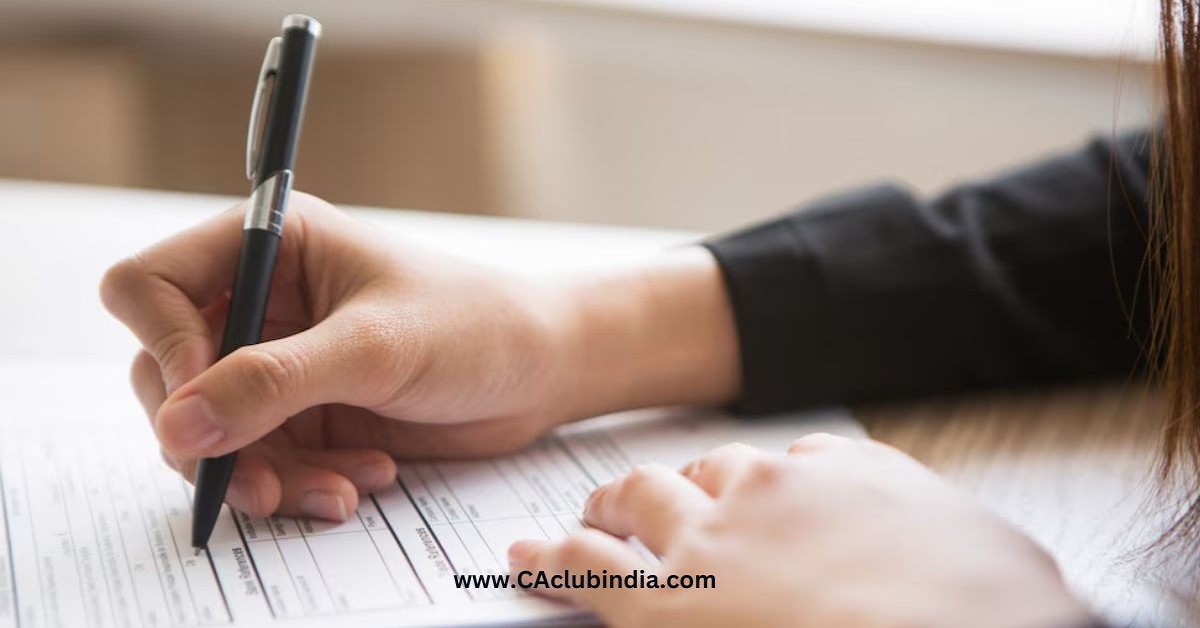
Production entries posting
The second step is to check the production entries for the particular period/batch/job/work that has been fully posted by the production team. It depends on the software or ERP package that the company is using. In an ERP system, the production process might be linked with your inventory and accounting module, and sometimes it's an isolated process, but as far as costing records, it needs to be checked that the required production entries have been posted fully in the software or system that the company is following.
Inventory posting & Updating
The next process is to check that all the inventories have been updated and are matching with the stores. All the inventories, such as raw materials, packing materials, consumables and finished goods, if any, need to be checked and ensured no entries are missed and left out without posting.
Materials cost ledgers closing
The next process that we need to check and update the materials cost ledgers and close the ledgers properly for the particular production period/batch/job/work. Most of the companies have their internal process within the ERP software system, and we need to run that process to close the costing ledger and check whether the particulars posted properly or not in the ledger.
Labour cost ledgers closing
The next process that we need to check and update the Labour cost ledgers and close the ledgers properly for the particular production period/batch/job/work. Most of the companies have their internal process within the ERP software system, and we need to run that process to close the costing ledger and check whether the particulars posted properly or not in the ledger.
Overhead ledgers closing
The next process that we need to check and update is all the utilities and conversion costs, such as power & fuel, water, steam, gas, etc., and close those ledgers properly for the particular production period/batch/job/work. Most of the companies have their internal process within the ERP software system, and we need to run that process to close the costing ledger and check whether the particulars are posted properly or not in the ledger.
Cost centres balance transfer
We need to check all the production-related cost center balances; if any are not transferred, In case there are any balances in the cost centre that are related to that particular production/batch/job/process/work, we need to transfer the same.
Bill of Materials variance checking
We need to cross-check the actual materials, labour, and utilities consumption with the standard bill of materials; this is required to check both in terms of quantity and price. This will help in analysing the costing variances of the companies that are following the standard costing system; it is automatic. However, whether your system is automatic or not, cross-checking the variances is important to ensure your production cost arrived correctly.
Calculate the cost of production
When we do the closing process after the completion of full production for the particular batch/job/service/process, we need to calculate the cost of production. The cost of production may be calculated over all levels or unit levels.
Calculate the work in progress
While closing the books when production is not fully completed or some uncompleted batch or process is in progress at the end of the period, we need to calculate the work in progress in terms of unit/percentage and also the value of the same; this is required for calculating the cost of production and preparation of costing & financials Profit & loss a/c
Preparation of Costing P&L A/c
The next step is to prepare the costing profit & loss a/c for the period for all the products produced during the period/process/batch/job/unit/work and calculate the profit or loss.
Reconciling with financial ledgers
The final step is to reconcile the difference between costing ledger details with financial ledgers and also analyse the profit or loss difference between financial P&L and Costing P&L.
The above checklist is prepared in general for the manufacturing and production industries and is not an exhaustive list. Based on the nature of the industry and process, it may vary.